During CNC vowin.cn/en/News/news1251.html' target='_blank'>machining, these thin-walled shell structures often cause a range of problems, such as warping and deformation. To overcome these issues, we try to offer serval process route options. However, there are still some exact issues for each process. Here are the details.
Process Route 1
In process 1, we start by machining the reverse side (inner side) of the workpiece and then use plaster to fill in the hollowed-out areas. Next, letting the reverse side be a reference, we use glue and double-sided tape to fix the reference side in place in order to machine the front side.
However, there are some problems with this method. Due to the large hollowing backfilled area on the reverse side, the glue and double-sided tape are not sufficiently secure the workpiece. It leads to warping in the middle of the workpiece and more material removal in the process (called overcutting). In addition, the lack of stability of the workpiece also leads to low processing efficiency and poor surface knife pattern.
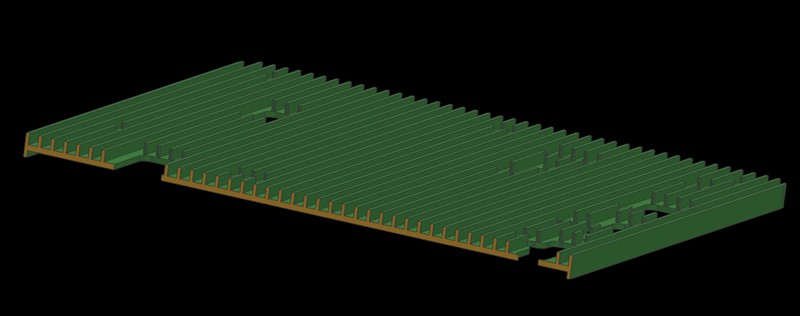
Process Route 2
In process 2, we change the order of machining. We start with the underside (the side where the heat is dissipated) and then use the plaster backfilling of the hollow area. Next, letting the front side as a reference, we use glue and double-sided tape to fix the reference side so that we could work the reverse side.
However, the problem with this process is similar to process route 1, except that the issue is shifted to the reverse side (inner side). Again, when the reverse side has a large hollowing backfill area, the use of glue and double-sided tape do not provide high stability to the workpiece, resulting in warping.
Process Route 3
In process 3, we consider using the machining sequence of process 1 or process 2. Then in the second fastening process, use a press plate to hold the workpiece by pressing down on the perimeter.
However, due to the large product area, the platen is only able to cover the perimeter area and could not fully fix the central area of the workpiece.
On the one hand, this results in the center area of the workpiece still appearing from warping and deformation, which in turn leads to overcutting in the center area of the product. On the other hand, this machining method will make the thin-walled CNC shell parts too weak.
Process Route 4
In process 4, we machine the reverse side (inner side) first and then use a vacuum chuck to attach the machined reverse plane in order to work the front side.
However, in the case of the thin-walled shell part, there are concave and convex structures on the reverse side of the workpiece that we need to avoid when using vacuum suction. But this will create a new problem, the avoided areas lose their suction power, especially in the four corner areas on the circumference of the largest profile.
As these non-absorbed areas correspond to the front side (the machined surface at this point), the cutting tool bounce could occur, resulting in a vibrating tool pattern. Therefore, this method can have a negative impact on the quality of the machining and the surface finish.