There are different types of knurling that product manufacturers use to create desired patterns on workpieces.
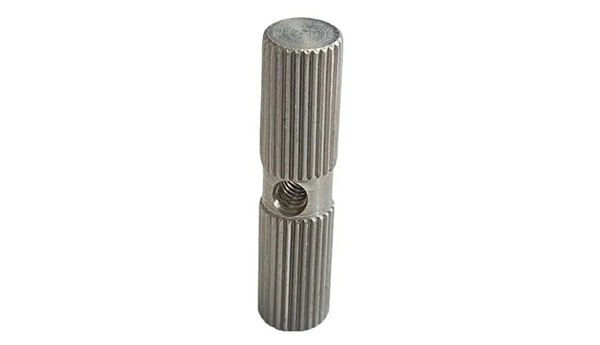
1. Straight Knurling
Straight knurling makes straight-line and groove patterns on the surface of a workpiece. It usually features intersecting parallel or diagonal lines made by a knurling tool with two hardened wheels with diagonal teeth. Moreover, many industries create straight knurling on products to give a patterned texture that improves gripping and handling.
Uses and Benefits of Straight Knurling
Decorative Purposes
Straight knurls are decorative patterns that add to the aesthetic appeal of a workpiece’s surface. It is perfect for cylindrical objects like handles and knobs. In addition, it is suitable for applications such as high-end writing instruments, custom hardware, or jewelry, giving it a stylish look.
Anti-Slip or Improved Grip Functionality
Straight knurling makes roughened texture on the surface of an object to enhance grip for easy object holding and manipulation. These knurling patterns help to increase friction between your hand and the workpiece, preventing slippage. It is beneficial in applications where a firm grip is crucial.
Alignment and Positioning
This knurling texture sometimes serves as a reference for component alignment and positioning. The patterns function as a visual indicator in aligning and adjusting components properly. Hence, straight knurling is ideal for equipment or mechanisms that need precise alignment, including fine-tuning mechanism, measurement tools, or optical devices.
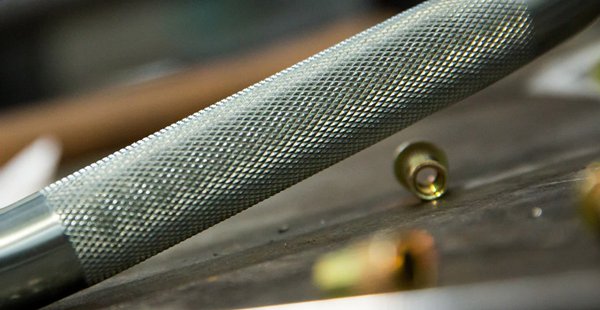
2. Diamond Knurling
Diamond knurling is another common type that makes small diamond-shaped ridges or indentation patterns on a workpiece’s surface. It usually consists of crossed-diagonal lines, forming several diamond-shaped projections. However, you can achieve this finish using knurling wheels with teeth arranged like a diamond.
Uses and Benefits of Diamond Knurling
Durability
The diamond knurls make a workpiece more wear-resistant and durable. They commonly apply to machine components, tools, or decorative pieces that experience consistent contact or high friction.
The diamond indentation or texture spreads the pressure and wears uniformly, reducing risks of wear or damage. Therefore, this attribute makes this knurling texture ideal for applications with high durability demands.
Decorative Application
The diamond-shaped indentation is unique and highly decorative. It produces complex and visually appealing knurling patterns on machined parts such as bicycle parts, lighter casings, or personal accessories to achieve an attractive and sophisticated appearance.
Improved Grip
Diamond knurling facilitates better grip in hand-held workpieces by creating several contact points between your hand and the workpiece. Since the diamond-shaped indentations aid better traction, you can easily grip and manipulate an object with this knurled finish.
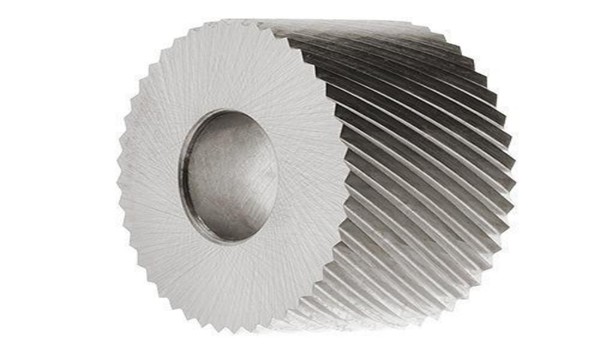
3. Helical Knurling
The helical knurling technique involves making diagonal lines in a whorl or spiral pattern on the surface of an object. Manufacturers typically use this knurling pattern on cylindrical surfaces, similar to a screw thread.
Uses and Benefits of Helical Knurling
Decorative Purposes
Helical knurling is similar to other types of knurling because it is also perfect for decorative purposes. You can combine it with decorative techniques like plating or polishing to improve your product’s overall appearance.
Enhanced Functionality
Helical knurling enhances the functionality of cylindrical parts like shafts, knobs, and handles. The helical knurled finish allows a firm grip in rotating and operating the machined part.
Thread Formation
It involves creating threads that match certain thread standards on cylindrical items. As a result, it reduces the need for further threading operations, making it a cost-effective and efficient process for specific applications.