Injection mold making is a complex manufacturing process, the process of making vowin.cn/' target='_blank'>injection vowin.cn/' target='_blank'>mold can be simply summarized as the following steps:
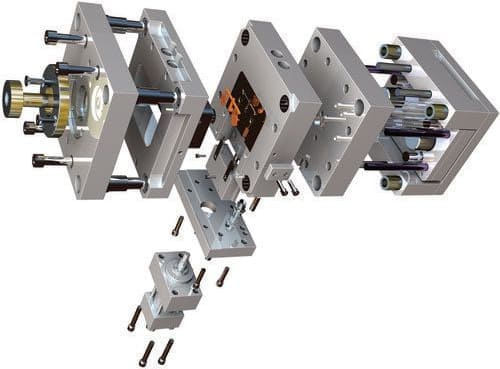
Step1: Get the sample or product drawing
Get the sample orproduct drawing of the plastic product to be injection molded parts by the customer.
When you get the sample, you can measure the points first, and then proceed to the next step. When you get the product drawing, you can proceed to the next step directly.
Step2: Make the plastic injection mold shape
Make the plastic injection mold shape, such as the mold with hot runner, design the hot runner as well.
Step 3: Confirm with the customer
Confirm with the customer after the mold is done.
Step 4: Purchase the material
Purchase the steel molds material.
Step 5: Rough machining
Roughing, rough machining, including dynamic and fixed mold line cutting, CNC milling, milling machine processing.
Step6: Finishing machining
Finishing machining, including medium-wire, slow-wire, high-speed milling, EDM, deep hole drilling.
Step7: Polishing
Polishing.
Step 8: Mold closes
Closing the mold, commonly known as the right touch.
Step 9: Final installation and commissioning
Final installation and commissioning. Debugging no problem, a pair of mold is complete.
Production time of injection molds
The production time of injection mold is related to the size and complexity of the product.
For products of conventional size and structure, the production cycle of injection molds is usually 25-30 days.
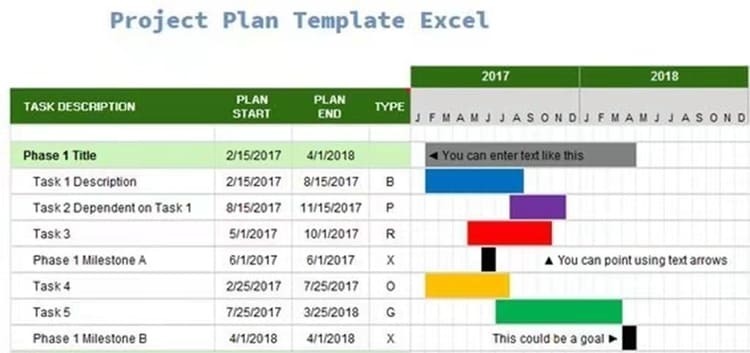
What is a plastic injection mold?
An injection mold is a tool for producing plastic products; it is also a tool that gives plastic products their complete structure and precise dimensions.
Injection molding is a processing method used for mass production of certain complex shaped plastic parts.
Specifically, the molten plastic is injected into the mold cavity at high pressure by an plastic injection molding machine, and then melted plastic cooled and cured to obtain an injection molded part.
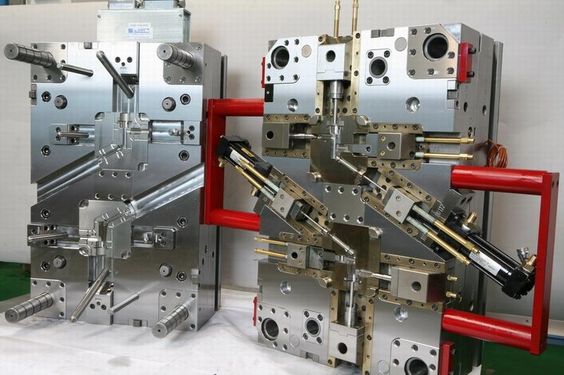
The development of plastic moulds
With the rapid development of plastic resin and plastic injection molding industry, plastic injection molded part also came into being at this time.
And now the quality requirements for plastic moulds are getting higher and higher, which provides a great impetus to the development of plastic mould industry.
The structural adjustment of plastic mould industry is accelerating, and the number and capacity of market-oriented professional plastic injection molder are also growing very fast.
According to the analysis of the production, sales, market situation, industry structure, products and import and export of plastic mould manufacturing industry, and with reference to the development trend of plastic mould related industries, the future development space of China’s plastic mould manufacturing industry is very broad.
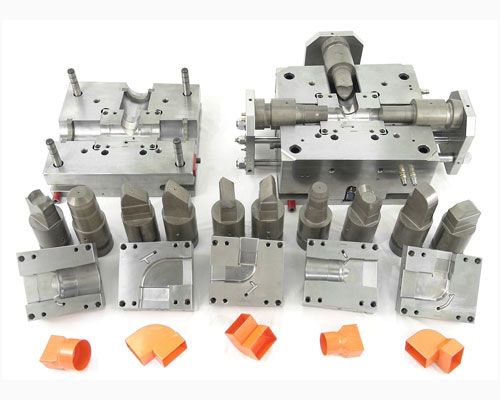
Injection mold composition
1) Plastic injection molding is the most commonly used method in plastics processing. The method is applicable to all thermoplastic material and some thermosets.
As one of the main tools of plastic injection molding process, the injection mold, in terms of quality precision, manufacturing cycle and production efficiency during the plastic injection molding process, directly affects the quality, output, cost and renewal of products, and also determines the responsiveness and speed of enterprises in the market competition.
2) The plastic injection molding tool is composed of several steel plates with various injection molded parts, which are basically divided into:
A. Forming device (concave die, punch)
B. Positioning device (guide post, guide sleeve)
C. Fixed device (I-plate, code die pit)
D. Cooling system (water hole)
E. Constant temperature system (heating tube, hot wire)
F. Runner system (choke hole, runner groove, runner hole)
G. Ejector system (thimble, ejector rod)

Classification of injection moulds by runners
Large spout mold
The runner and gate are on the parting line, and the product is demolded together when the mold is opened, the design is the simplest, easy to process with low cost, so more people use the large spout system to work.
Fine spout mold
The runner and gate are not on the parting line, generally directly on the product, so to design more than one group of spout parting line, the injection mold design is more complex, plastic injection molding process is more difficult, generally depending on the product requirements and the choice of fine spout system.
Hot runner mold
The runner and gate are not on the parting line, generally directly on the product, so to The runner and gate are not on the parting line, generally directly on the product, so to design more than one group of spout parting line, the injection mold design is more complex, plastic injection molding process is more difficult, generally depending on the product requirements and the choice of fine spout system.
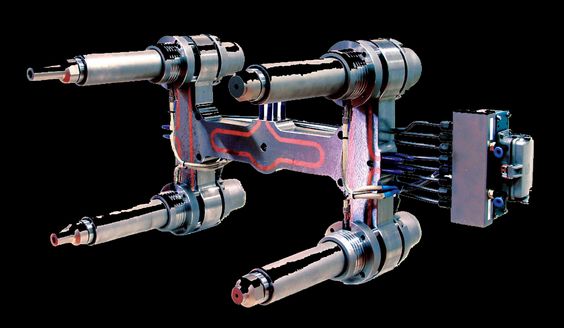
Injection mold manufacturing can be roughly divided into the following steps
Process analysis of plastic products
Before the injection mould design, the designer should fully analyze and study whether the plastic products conform to the principle of injection molding processes, and the designer of the product needs to negotiate carefully, and a consensus has been reached.
Including the product geometry, dimensional accuracy and appearance requirements, necessary discussion, as far as possible to avoid unnecessary complex mold manufacturing.
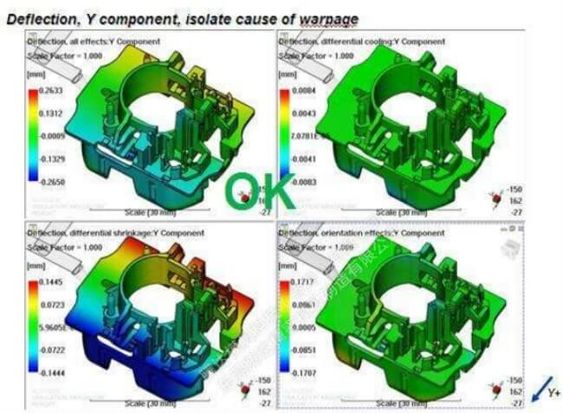
Mold structure design
Before the injection mould design, the designer should fully analyze and study whether the plastic products conform to the principle of injection molding processes, and the designer of the product needs to negotiate carefully, and a consensus has been reached.
An excellent mold designis: on the premise of meeting the requirements of customers, so tha the processing cost is low, the processing difficulty is small, the processing time is short.
To do this, not only to fully digest the customer’s requirements, but also to understand the injection molding machine, mold structure, processing technology and mold factory’s own processing capacity.
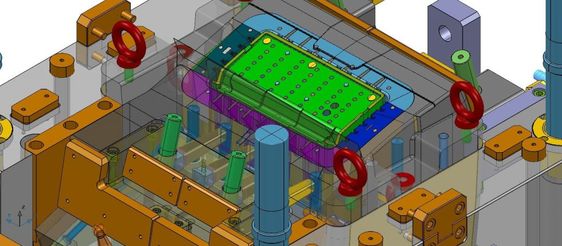
Therefore, to improve the level of mold design, the following points should be done
1. Understand every detail in the design of each mold and understand the purpose of each part in the mold.
2. Refer to previous similar designs in the design, and understand the situation of mold processing and product production, and learn the experience and lessons.
3. Learn more about the working process of injection molding machines to deepen the relationship between mold and plastic injection molding machine.
4. Go to the factory to understand the process of processed products, and understand the characteristics and limitations of each process.
5. Understand the mold test results and mold modification of the mold designed by myself, and learn lessons.
6. Try to use the previous successful mold structure in the design.
7. Learn more about the impact of mold water on products.
8. Study some special die structure and understand the latest die technology.
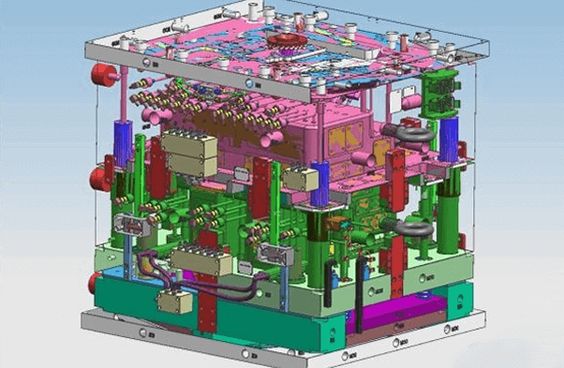
Determine the mold material and choose standard parts
In the selection of mold materials, in addition to the accuracy and quality of the product to consider, but also combined with the actual ability of the mold factory processing and heat treatment to give the right choice.
In addition, in order to shorten the manufacturing cycle, as far as possible to use the existing standard parts.
Parts processing and mold assembly
In addition to the accuracy of the mold in the design to give the best structure and reasonable tolerance fit, parts processing and mold assembly is essential.
Therefore, the processing accuracy and processing method of choice in the injection mold manufacturing occupies an absolutely dominant position.
The dimensional error of the molded products is mainly composed of the following parts
1.the manufacturing error of the mold is about 1/3
2.mold wear caused by the error of about 1/6
3.The error caused by the uneven shrinkage of the molded parts is about 1/3
4.The error caused by the inconsistency between the scheduled shrinkage and the actual shrinkage is about 1/6
Total error = (1)+(2)+(3)+(4)
Therefore, in order to reduce the injection mold manufacturing error, the first should improve the processing accuracy, with the use of CNC machine tools, this problem has been well controlled.
In addition, in order to prevent the error caused by mold wear and deformation, the cavity, core and other key parts should be quenched when processing molds with high precision requirements and large product output.
In the medium and large mold, in order to save material and facilitate processing and heat treatment, mold design should be used as far as possible to put together the structure.
In order to solve the uneven shrinkage of the injection molded part and the scheduled shrinkage and the actual shrinkage of the error arising from inconsistency, in the injection mold manufacturing generally choose the product tolerance of 1/3, as the mold manufacturing tolerance.
The purpose is to give the molding process in the future to leave a larger adjustment margin, in order to solve the error caused by the molding process.
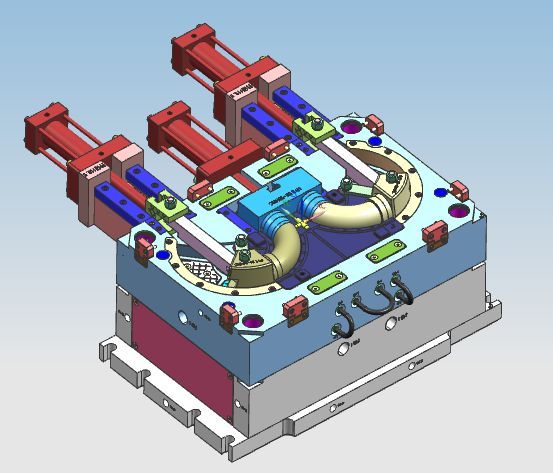
Test mold
A set of mold from design to assembly is only 70%~80% of the total manufacturing process.
For the error caused by the inconsistency between the intended shrinkage and the actual shrinkage, the smoothness of the mold release, the cooling effect, especially the size, position and shape of the sprue on the precision and appearance of the product, etc., must be tested through the mold trial, so It is very important for injection mold factories to have their own injection molding machine for the mold trial process.
Therefore, mold trial is an indispensable step to check whether the mold is qualified and choose the best injection molding processes.
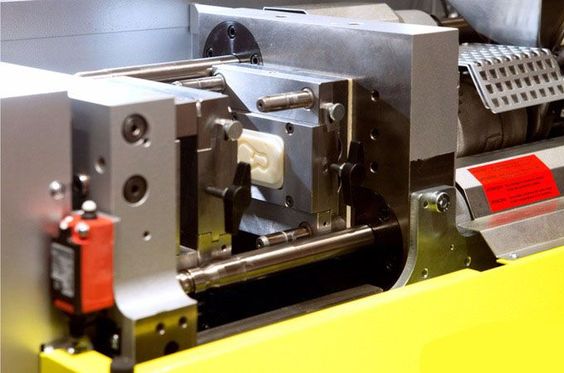
The advantages of using injection molds
A lot of heat is needed in the plastic injection molding process. The best way to ensure that every finished product is fully molded is to have a reliable mold that can handle high and low temperatures without affecting the shape of the final plastic part.
The following are the advantages of using metal molds for plastic injection molding process.
They are durable and can be used for a long time. Molds made of aluminum or steel are very strong and can take quite a few knocks before they fail.
This could be many years from now, giving you plenty of time to make the most of them.
They can handle high and low temperatures, which makes it easy to design any shape without distortion.
The raw materials being injected into the crates are usually very hot and if the molds have a low melting point, they may melt in the process and contaminate the entire batch.
The development time is much faster, especially for the cooling part. This is due to the fact that metal parts is a good conductor of heat.
Once the molten material is spread evenly, the mold can dissipate heat quickly, speeding up the cooling process.
The mold can be reused for a long time without any change in the overall design.
Metals are highly resistant to extreme changes in heat and cold, which is what makes plastic injection molding such a reliable process for mass production of large and small items.
A good and reliable mold will reduce production costs, especially if you are dealing with large scale production.
The repeatability it gives to the manufacturer means a better use of raw materials and a decrease in energy consumption because there is no interruption in the process.
If you want to change the shape of the design, you can do so at any time. Molds can be made larger or smaller depending on your needs, and this flexibility is another added advantage that makes production easier and faster.
The ability to change a design without having to start over is an underrated accomplishment.
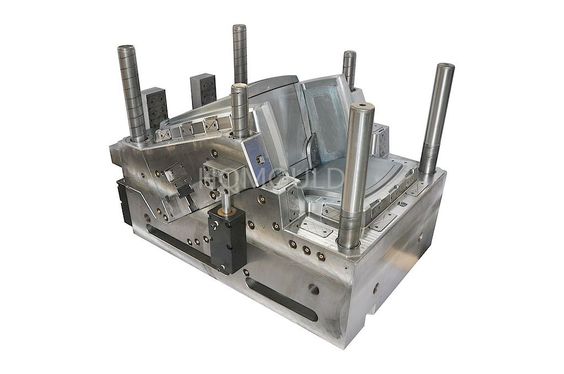
Limitations of using injection molds
As good as it may be, using molds for plastic injection is not without its limitations. Although the pros far outweigh the cons, there are still some things you have to be careful about if you choose to go down this path.
The initial cost of building a mold is very high, and if you plan to run multiple assembly lines, the tooling costs can be at its highest point.
In fact, this production model only makes sense for high volume production. Dealing with a small number of people will only lead to a waste of resources.
There are design limitations because modifications cannot be too large. Once the die is set, there is little room for flexibility.
You can only make limited modifications; the only way you can change the entire design is to make a completely new plug-and-play mold.
CNC machining costs are very high. For example, it can cost thousands of dollars to run a CNC machine, which is more than a small business can handle.
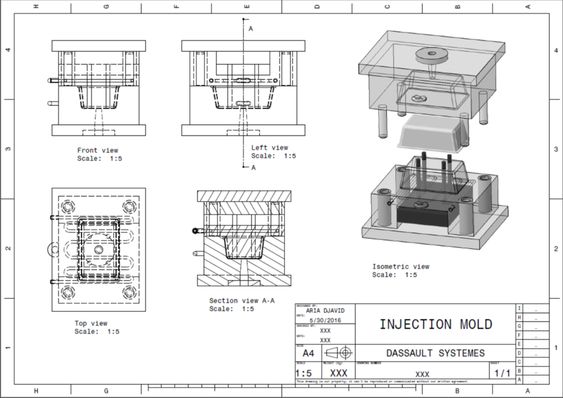
Why we choose injection molds?
High efficiency
Plastic injection molding is known as one of the most commonly used technologies for long production periods because it is very fast.
But, how fast? Though its production speed may be dependent on the complexity of the mold structure, there is only about 15 to 30 seconds interval between injection molding cycle times.
High precision
As a highly accurate processing approach, the injection molding process is able to be used to produce diversified plastic parts of almost any types.
Though certain design restrictions do exist, the injection molds are made to ensure the great precision of the molded products.
As a matter of fact, the precision of the finished products can be kept within 0.005in.tolerance.
Highly resourceful
Today, many people are concerned about sustainability, so product developers often choose a process that helps the environment and eliminates waste.
Plastic injection molding is not only an efficient and effective process, but it is also a very flexible one.
The reason is that only the required amount of plastic is used to produce the desired product; the excess material is recycled.
It saves the labor cost
The injection molding equipment requires minimal human supervision, of which the reason is that they usually work with a self-gating and full automatic tool, so as to realize streamlined operation and continuous production.
It’s flexible
In addition, the plastic injection mold making process is not only accurate, it also features great flexibility.
It means that it is very easy for us to change the material type as well as the color for our production once we made a mold. also when you want to change the shape of the product, we just need to remove or add some steel to achieve it.
Lighter and cheaper
The density of the plastic material is much lower than metal, and plastic injection molding is one-time shaping process without secondary operations. so it is much cheaper than metal.