We make low to medium volume production in plastics, metals and silicones uniquely affordable. If you are looking for low to medium runs, then you have come to the right place! Our inexpensive rapid tooling for runs up to 100,000+ injection moulding parts may be exactly what you need. We continually invest in the latest equipment and rapid manufacturing technology and this, combined with our experienced staff, means that we are well equipped to handle low to medium-volume production programs.
What is Silicone Compression Molding?
Silicone Compression molding is a process where heat is used to create silicone rubber component, the rubber material is placed into a mold cavity. Then the mold is closed and held at a certain temperature, where it takes the shape of the mold. The work process is similar to plastic injection moulding. After cooling and trimming of any excess material, the end result matches the design you create.
Most of parts with a wide array of lengths, thicknesses, and complexities can be produced by this process. The components are also high in strength, making it an attractive process for a number of different industries.
How Does Compression Molding Work?
You can see below pictures, it explains the work process of na.
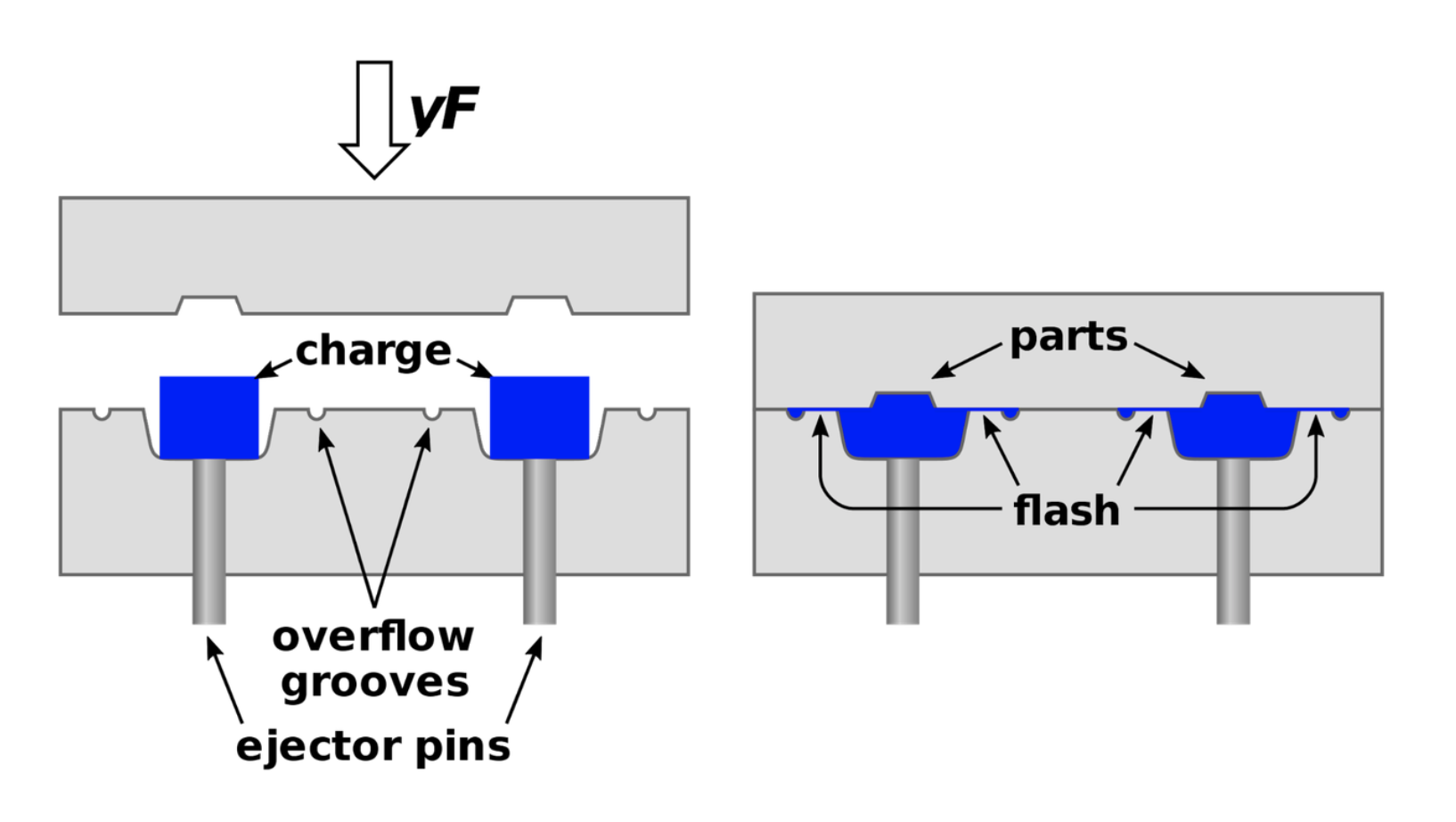
Also, there are four main steps of Compression Molding Process:
Step 1: Created a high-strength, two-part metal tool that exactly matched the dimensions required to produce the required parts. The tool is then installed in a press and heated.

Step 2: Pre-form the required composite material into the shape of the tool. Preforming is a crucial step, helping to improve the performance of the finished part.
Step 3: The pre-formed part is inserted into the heated mold. The tool is then compressed under very high pressure.
Step 4: After releasing the pressure, remove the part from the tool. At this time, all resin burrs around the edges will also be removed.
Benefits of silicone compression molding
#1 Cost effective in tooling
#2 Fast turnaround in cutting the tooling (sometimes in hours or a few days)
#3 Effective for a large or low volume parts
#4 Can create very complex parts
#5 Use advanced composites. These materials tend to be stronger, stiffer, lighter, and more resistant to corrosion than metal parts, resulting in superior objects.
What's kind of material can be used in Compression Molding?
Thermoplastic materials are types of plastics that become soft and pliable when heated and harden when cooled.
* EPDM
* Silicone
* Urethane
* Polyurethane (PU)
* Polytetrafluoroethylene (PTFE)
* High-density polyethylene (HDPE)
The Applications of Silicone Compression Molding
Silicone Compression molding is the oldest method that used to mold silicone prototype rubber parts. And it has a wider appliance in automotive, aerospace, medical, make-up and electric digital industries, baby products and houseware etc...
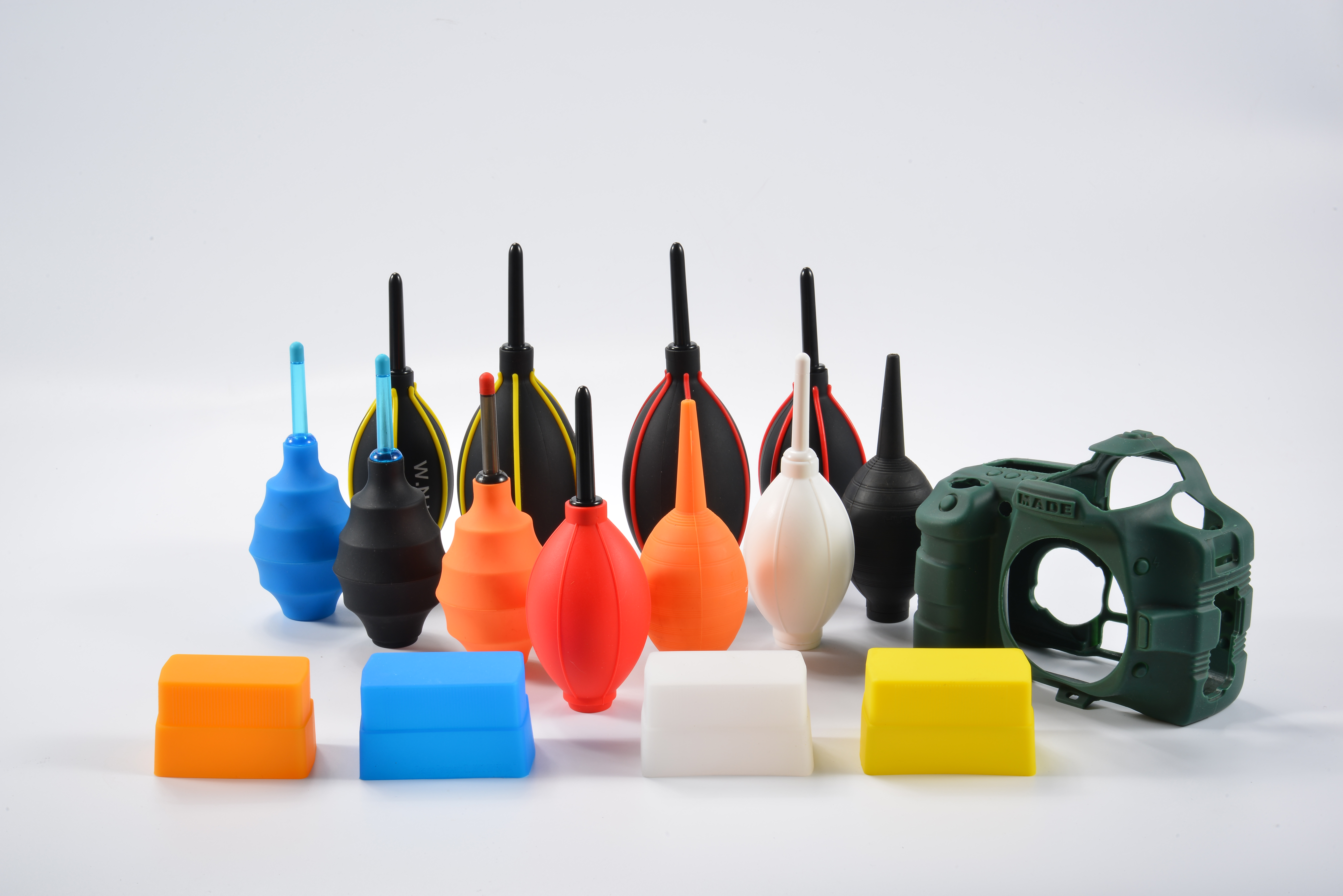
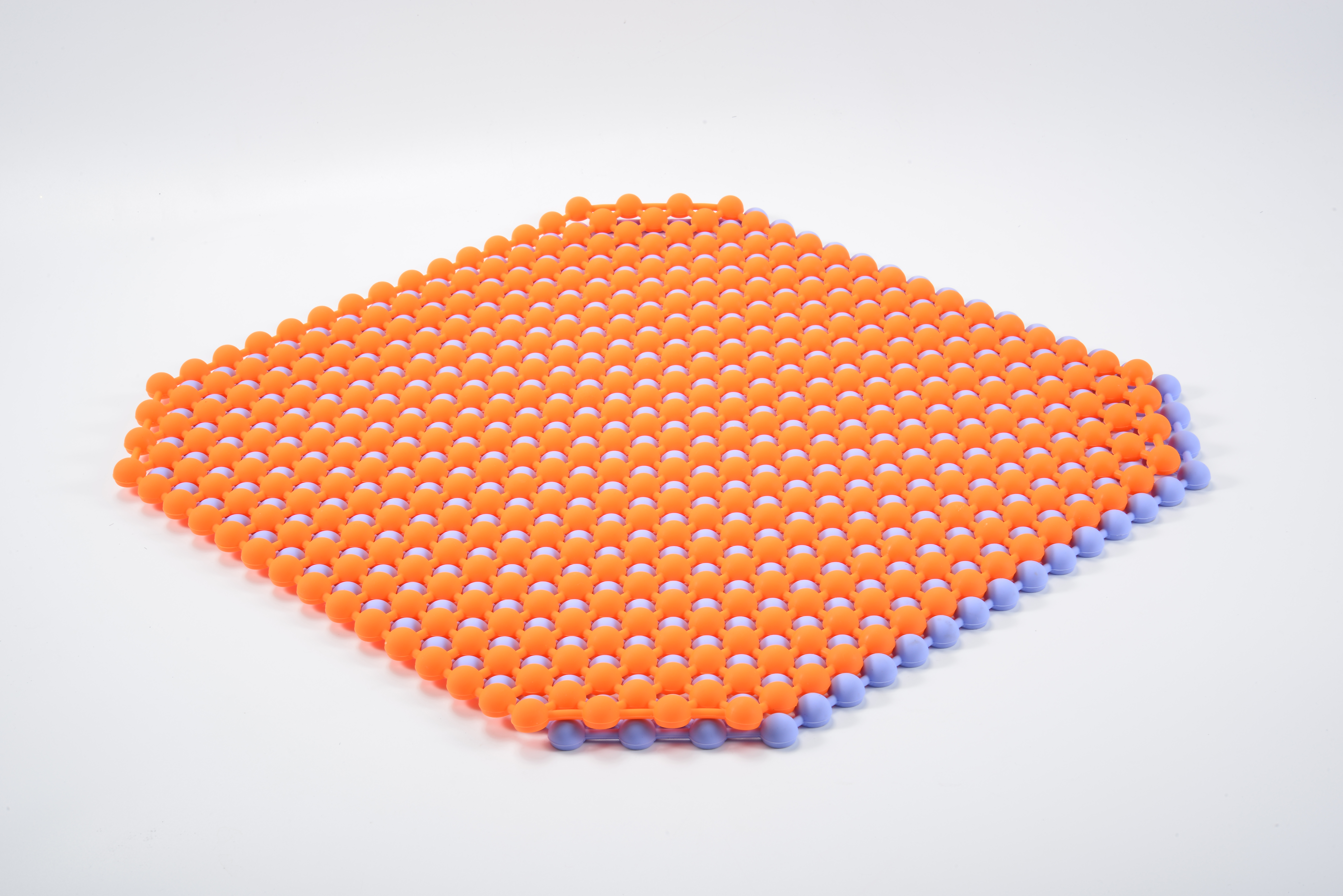
Compression Molding VS Injection Molding
Compression molding is very similar to injection moulding, but they have one major difference. Molds are closed around the charge in compression molding, and the charge is injected into a closed mold cavity while in injection moulding.
To manufacture different types of components, many manufacturers will adopt both compression molding and injection moulding method. However, for these large parts that cannot be produced using extrusion techniques, compression silicone molding China is a better choice.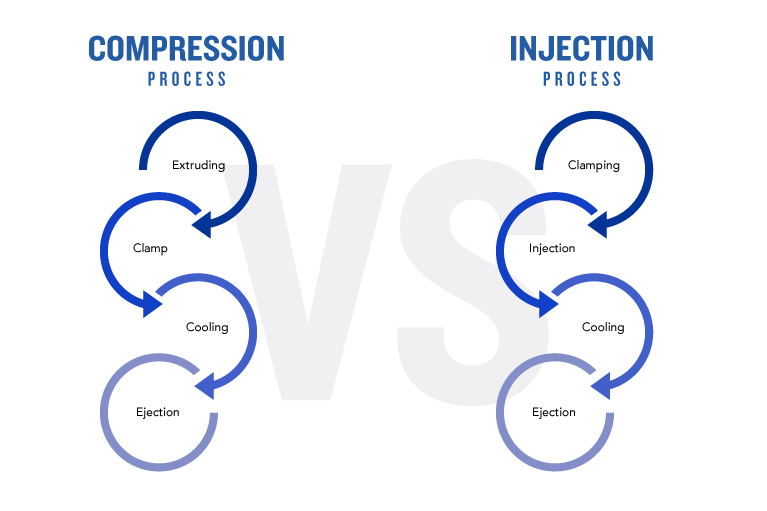
Injection moulding has a shorter cycle time than silicone compression molding, it has the advantage of faster and more cost-effective when producing a large number of parts. However, silicone compression molding is suitable for lower-pressure production, so the tooling costs are often lower. It also wastes little material and can provide an advantage when working with other expensive materials.
Summary, injection moulding is suitable for high volume production while silicone compression molding is used rather for low and medium production.