Plastic injection molding is a process where molten plastic resin is injected into a heated steel mold cavity by injection molding machine that has been shaped to the desired part. Designers have to take many factors into consideration when designing product for this design process and manufacturing process.
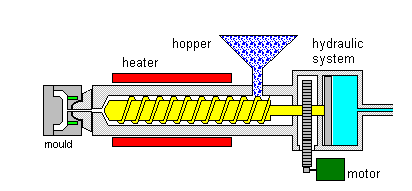
Figure 1